Sifter Mesh
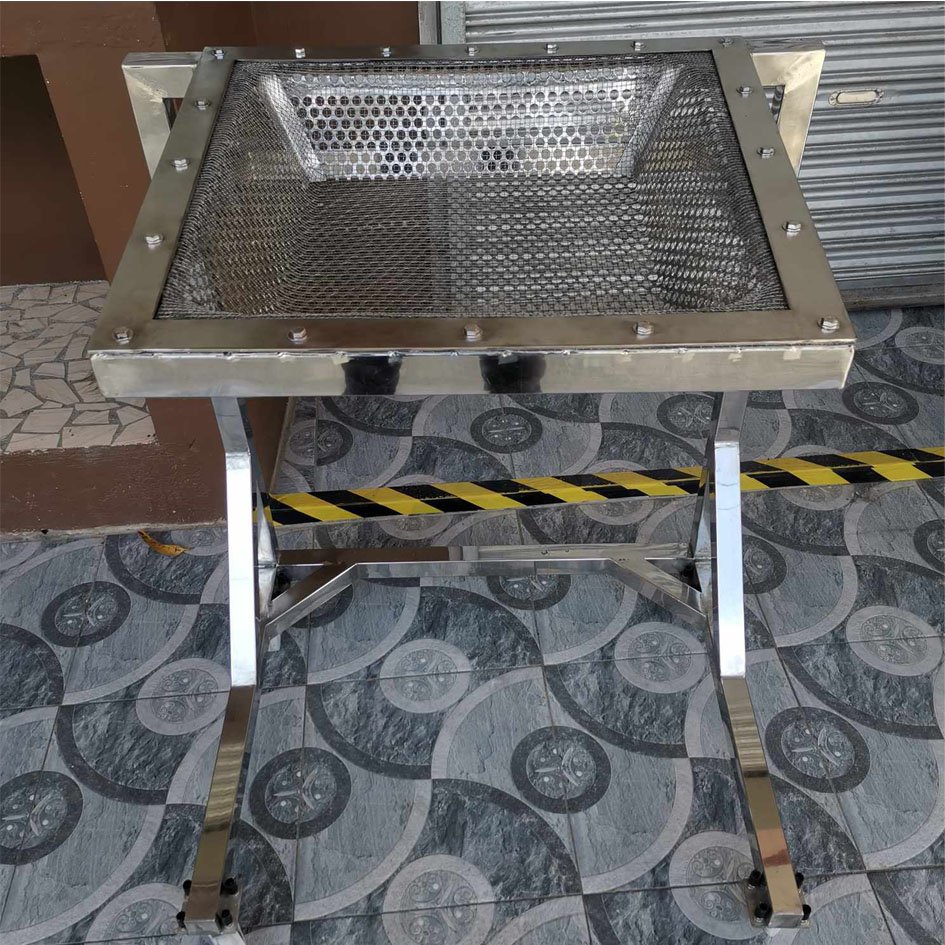
Fabricating a sifter mesh involves creating a fine mesh screen typically used in sifters, sieves, or similar devices for separating particles of different sizes.
Here are general steps for fabricating a sifter mesh:
Material Selection:
- Choose a material suitable for your application. Common materials for sifter mesh include stainless steel, aluminum, or nylon, depending on factors like durability, corrosion resistance, and the type of particles being sifted.
Mesh Design:
- Determine the required mesh size based on the particles you want to sift. Mesh size is defined by the number of openings per linear inch or other standardized units.
Cutting the Material:
- Use appropriate cutting tools to cut the selected material into the desired shape. This often involves creating a frame or border for the mesh.
Mesh Weaving or Welding:
- Depending on the material and specifications, weave or weld the mesh onto the frame. Weaving is common for metal meshes, while welding may be used for certain materials like stainless steel.
Frame Construction:
- Construct the frame to hold the mesh securely. The frame can be made from the same material as the mesh or a different material, depending on the application.
Securing the Mesh:
- Ensure that the mesh is securely attached to the frame. This may involve welding, binding, or using other fastening methods to prevent the mesh from detaching during use.
Surface Treatment (Optional):
- Depending on the material and application, consider surface treatments such as coating or plating to enhance corrosion resistance or improve other properties.
Quality Control:
- Inspect the finished sifter mesh for any defects, irregularities, or inconsistencies. This may include checking the mesh size, ensuring proper attachment to the frame, and overall structural integrity.
Packaging and Distribution:
- Once the sifter mesh passes quality control, package it appropriately for distribution. Consider providing instructions for proper use and maintenance if necessary.